It looks like some exotic piece of machinery for exo-planetary exploration, but in reality it is a futuristic concept cooked up by Volvo Construction Equipment of what an automated road paver in the third decade of this century might look like.
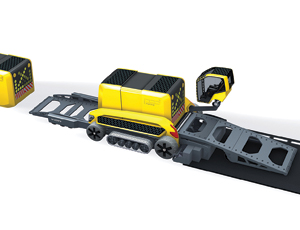
The Swedish construction equipment builder unveiled a model of its “Fenix” asphalt paver in late April at the Intermat equipment show in Paris. Volvo emphasizes that Fenix is only a concept at this point. The asphalt-paving process normally is a process involving “a lot of labor, a lot of machines, a lot of management, a lot of fumes and a lot of energy,” says Lorenzo Terreno, Volvo Construction’s advanced engineering coordinator for the project. Fenix would put a single operator in an air-conditioned cab controlling a machine that would carry out all these functions more efficiently.
The Swedish company’s engineers envision Fenix to be powered by a hydrogen fuel cell to eliminate emissions and even noise, says Volvo. The paving system consists of a central crawler-mounted ramp with a height- and angle-adjustable cab on one side. Instead of being delivered in dump trucks, hot-mix asphalt is transported from plants in thermopods that are placed at 50-meter intervals ahead of the moving Fenix. Each pod holds 17 tonnes of mix at 135° C for up to three hours.
The mix is unloaded from the pod and moved by conveyor to Fenix’s auger chamber, from which it is laid on the paving area at rates matched to the paver speed and depth requirements. The operator monitors all paving and compacting functions via sensors. The machine can even paint lines on the fresh asphalt.
The thermopods are equipped with GPS technology, keeping everybody in the loop about the pods’ exact location and time of arrival at the site. Once emptied, the containers collapse automatically into a space-saving size for transport.
In another nod to the environment, Fenix’s hydraulics use distilled, de-ionized water instead of oil. It is less expensive, more energy efficient because of water’s low viscosity and leakage would not be hazardous, according to Volvo.
The project goes back to Volvo’s 2007 acquisition of Ingersoll Rand’s road machinery business. This led to a meeting in October 2008 of a small team of senior managers, engineers and industrial-design specialists. The Fenix vision emerged six months later.
Post a comment to this article
Report Abusive Comment