With an installed capacity of over 10,500 MW, India is currently the fifth-largest generator of wind power in the world. As it adds about 1,200 MW of wind capacity per year, the potential is far from depleted, but developers are faced with challenges in erecting the turbines in remote areas.
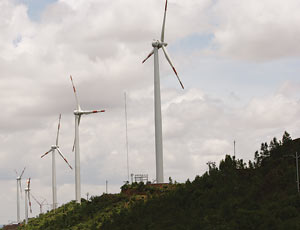
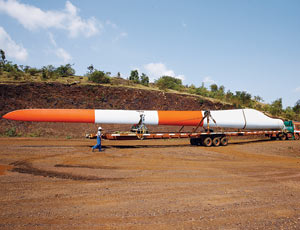
Unlike their Western counterparts, Indian developers often must find innovative means to transport large turbines through narrow, crowded roads to ill-equipped, hilly sites. “Non-availability of transport and cranes, lack of experienced manpower and infrastructure [lacking] such things as cement mixers, electrical lines, substations, new roads and cables, distinguish India from its Western counterparts,” says a spokesman for Pune-based Suzlon Energy, the world’s fifth- largest wind turbine maker.
Most wind farms are located in remote areas, and curved winding roads to the hills pose a logistical nightmare, says M. Chandrashekhar, general manager of logistics for ReGen Powertech, a Chennai-based wind developer. In addition, in India it is illegal to transport large elements such as turbine blades by truck, so it becomes necessary to “go around” the rules by transporting equipment at night, says an observer.
“We often have to build three to four kilometers of roads or by-passes through villages in certain locations in the hills of Andhra Pradesh in South India that pose different challenges,” says Chandrashekhar.
With infrastructure on sites limited, Enercon India recently set up an 8,000- sq-meter tent to house a mobile prefab concrete-tower factory for its 800-kW turbines in the western state of Gujarat. Transporting prefab towers in the remote, undeveloped region is difficult.
Towers will be produced in 18 segments; each will have a 5.50-m base diameter and a tower-top diameter of 1.80 m. A tower crane in the center distributes concrete in the production area. A mobile concrete mixer also is used to provide concrete for the foundations, ensuring a uniform quality of concrete.
“We now have a production plant which we can set up anywhere in the world within a short period of time,” says an Enercon spokesman.
Post a comment to this article
Report Abusive Comment