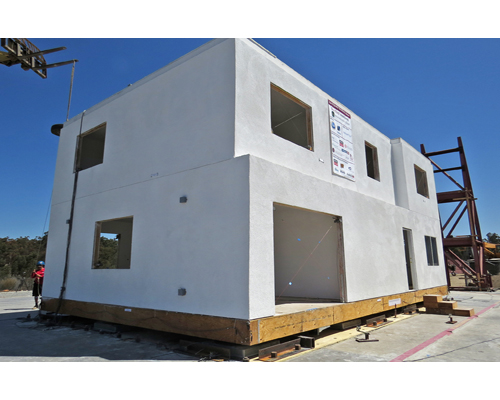
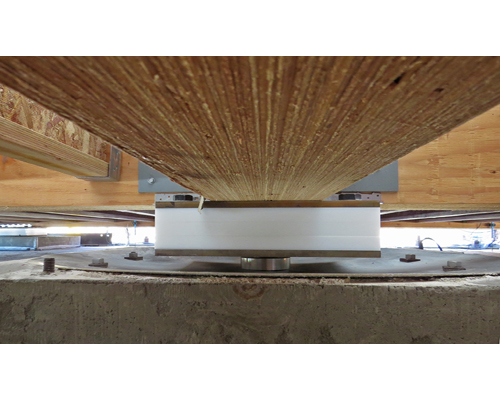
Recent shake-table tests on a wood-framed house—equipped with newly developed low-cost seismic base isolators—confirmed predictions that the two-story house would come through structurally unscathed. The goal of the research, considered an important step toward more earthquake-resilient single-family housing, is to "dramatically improve" the seismic performance of light-frame residential construction, without making the houses uneconomical.
"Seismic isolation is not a new concept, but it has been cost-prohibitive for houses," says Gregory Deierlein, a professor of civil engineering at Stanford University and one of three principal investigators in the three-year research program on earthquake-resilient housing. "The key is to make it inexpensive," says Deierlein, whose co-principal investigators are Stanford engineering professor Eduardo Miranda and California State University, Sacramento, professor Benjamin Fell.
While well-designed and well-constructed wood-frame houses typically will meet code-required performance in a quake, the performance target is focused on protecting the life of the occupants and allowing them to exit the building safely. Though traditionally framed residential structures provide a high level of life safety during a quake, their vulnerability to damage can be very costly. After the 1994 Northridge quake, insurance payouts for damaged residences reached an estimated $20 billion, according to the researchers. In addition, over 60,000 people were displaced from their homes for a significant period of time.
To reduce the damage in future quakes, current design standards must be revised to prevent the ultimate load from being reached at large, damaging drifts, the researchers agree. Toward this end, they are developing a new seismic design methodology to reduce deformations and damage through an enhanced-strength-stiffness, limited-ductility, light-frame, shear-wall system. The combination of creating unibody-type construction to strengthen the superstructure using low-cost isolation to separate the structure from the ground addresses the challenges of reducing quake damage in a typical house, say the engineers.
"We are taking a separate route, which is contrary to conventional practice of providing ductility," says Deierlein. "Houses don't need that much ductility, provided they are stiffer and stronger."
The $400,000 testing program—called Seismically Isolated Unibody Residential Buildings for Enhanced Life-Cycle Performance and conducted at the shake-table laboratory at the University of California, San Diego's Network for Earthquake Engineering Simulation—represents the culmination of a $1.3-million National Science Foundation project. The tests shake a full-scale, seismically isolated structure, first with sliding dish-shaped isolators, then with sliding flat, hockey-puck-like isolators. Dish isolators recenter the structure; flat isolators don't.
Earlier this month, the first two series of tests on the isolated house "substantiated our predictions," says Deierlein. Control tests on the fixed-based condition, which will include shaking to collapse, will take place this week.
At the crux of the project is the development of isolators that are more economically viable than conventional isolators because they are made from less-costly materials, including galvanized plates and high-density plastic. The less-expensive materials are appropriate for lightweight framing because the vertical bearing pressures on houses are lower than on buildings with heavy framing, says Deierlein.
The test house is framed using 2x4s and joists. Instead of the more common plywood shear walls or braces, the engineers created stiff and strong walls by attaching the gypsum board with structural adhesives. Each test series included 15 shakes that mimicked the force of the code's maximum considered earthquake or above. The house was essentially undamaged, says Deierlein.
Rene Vignos—a principal with seismic structural engineer Forell/Elsesser Engineers Inc., which is an industry partner on the project and an adviser to the researchers—says the research "represents an important step by demonstrating what is possible. It is focused on ways of modifying current house design and construction techniques to reduce damage, instead of inventing a brand-new construction method that would have slower acceptance in the market."
Retrofitting existing houses might be expensive, says Deierlein. He estimates that, for new construction, the isolation might add about $15,000, or less than 4% to the cost of a $400,000 townhouse.
"If you isolate your house, you probably won't need earthquake insurance, which few people have anyway," says Deierlein. Insurance costs about $1,000 annually, and the deductible can be 20%, he adds.
Vignos expects some resistance from homebuilders and contractors to the extra expense of the isolated system. "If the benefits of reduced damage can be communicated to the homeowner and to insurance companies in a clear and understandable way, the supply of this type of construction could be driven by homeowner demand and reduced insurance premiums," he says.
Post a comment to this article
Report Abusive Comment