During his tenure at the National Aviation and Space Administration, Craig Collier helped develop the software that would become HyperSizer, a computer-aided program for designing with composite laminates. When he left NASA, his brainchild followed him— sort of—into a project with NASA to commercialize the product with the recent release of HyperSizer v6.
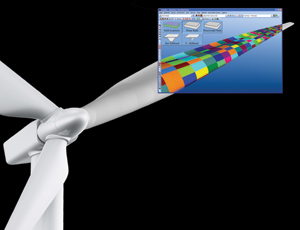
HyperSizer is designed to help bridge the capabilities of CAD software and finite element analysis (FEA) to test objects that are made with composite materials, which can include metals, alloys and plastics. The product does this by automating what would otherwise be manual calculations in stress analyses. When it comes to testing new components, the product can be a key feature of any project.
“There is a no-failure tolerance in NASA,” says Collier, now president of Collier Research Corp., Hampton, Va.
Collier works with HyperSizer by taking a 3D CAD model of objects designed with composites, then defining how the elements relate geometrically. Next, he plugs in FEA techniques to predict what will happen to the mixed materials under stresses, such as pressure or heat.
When high-performance structures are designed with mixes of metals and plastics, they can be light and strong. “But predicting what they will do under stress can be difficult,” says Collier. “HyperSizer predicts what will happen to composite materials under different stresses and suggests alternatives.”
Ian Fernandez, a NASA employee and project lead on the Lunar Atmosphere and Dust Environment Explorer (LADEE), is using the software to analyze composites in the vehicle before its 2013 launch.
Collier and Fernandez also collaborated to analyze design options with HyperSizer a few years ago while working on a Composite Astraunaut Module. “We came up with a design—for the bottom part—that was 30% lighter than traditional pressure shells,” says Fernandez. “Using HyperSizer was a big part of doing that.”
Fernandez says he is using HyperSizer on LADEE for sizing optimization calculations to determine the lightest-weight material combinations possible. “Our FEA is linked to CAD, and we incorporate the material properties that are being developed. HyperSizer generates all of the safety margins on the vehicle.”
Tom Ashwill, an engineer at Sandia Corp., Albuquerque, N.M., is test-modeling a 100-meter-long wind-turbine blade built with new composites using HyperSizer. With HyperSizer’s analysis of the composites, Collier hopes to make the blade a reality.
Licensing fees for the software start at $4,000.
Post a comment to this article
Report Abusive Comment