Some skilled equipment operators have a sixth sense that allows them to focus on the task at hand while maintaining awareness of the bustling, often unpredictable activity going on around them. Unfortunately, no operator has yet developed X-ray vision that allows a viewpoint through engine cowlings, cab framing and other obstructions.
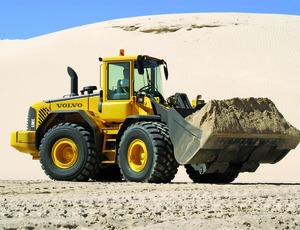
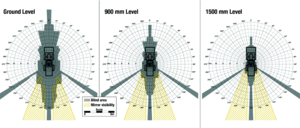
Such blind spots have contributed to hundreds of deaths at roadbuilding sites over the past 15 years, according to the National Institute for Occupational Safety and Health (NIOSH). Fatalities involving a ground worker being struck by a vehicle or equipment account for 73% of transportation-related work zone incidents, with half occurring when a construction vehicle was backing up.
Technology and training are not the only solutions to this problem, experts say. Relying on the operator's attentiveness and back-up alarms is not sufficient to prevent these injuries.
“With noise coming from all directions, workers may not know where the alarm is coming from—assuming they can hear it at all,” says Michael McCann, former director of safety research for the Center for Construction Research and Training. He adds that employing spotters to alert drivers of the dangers can improve safety, “but they become at risk of being hit by another machine.”
Over the past decade, NIOSH has studied the problem and developed new diagrams that depict the area around a vehicle that an operator cannot see. These maps have been developed for more than 40 pieces of heavy equipment using an International Organization for Standardization (ISO) test method.
“The unique component of what we did is the development of blind area diagrams at three different elevations,” says David Fosbroke, a statistician for NIOSH's Division of Safety Research in Morgantown, W.Va. Along with the ISO standard ground-level map, NIOSH added diagrams at 900 mm, the height of most construction barrels, and 1500 mm, which is the shoulder level of the 95th percentile female.
The tallest level “represents the height at which enough of a person's head is visible to be recognized by an operator,” Fosbroke says.
Though blind areas tend to increase in step with machine size, Fosbroke says some blind spots are machine-specific. Smaller machines, like skid-steer loaders, tend to have poor visibility. Larger shuttle buggies have an especially large blind area forward and opposite the operator seat.
Other factors include the size and shape of vehicle components and attachments, the position of the operator's station and the focus of the operator's attention. As such, a blind area may vary depending on where the operator is positioned when running the machine.
For example, compactors typically have very good visibility. However, when the operator is working an edge of the road below, “the entire area behind him or her becomes a functional blind area,” Fosbroke says.
Post a comment to this article
Report Abusive Comment