A typical job for the Bocell brothers starts with a phone call. “Nothing else had worked. Figured we’d give it a shot,” says Stanley Wondolowski, manager at a Corpus Christi, Texas, condominium association, recalling the day he dialed the Bocell’s number. “Every time it rained, it was a swimming pool down there.” CGI Texas, Dallas, knew how to handle the leaky concrete parking structure. “They drilled holes in the concrete, shot this gel into it, and the leaks stopped. It was very successful,” says Wondolowski.
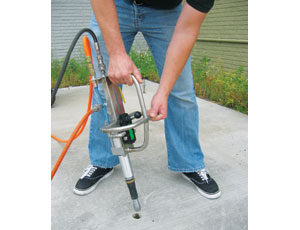
CGI Texas is run by Marshall, James and Ben Bocell. They get plenty of calls to fix leaks—and not just in Texas. “We were in New York City working on the World Trade Center 7 elevator pit a while back,” recalls Marshall Bocell. “It was leaking from everywhere: floors, walls. We took care of it.”
The “gel” used by CGI Texas is a quick-set, two-component resin developed by Claude Gosselin, a French chemist who licenses it to CGI Texas through his own firm, DSI Resin. The unique “pistol” used to directly inject the resin into porous, cracked or leaking concrete was developed by Marshall Long, the Bocell brothers’ grandfather. How it all came together is a bit of family history.
Marshall Long was an engineer. A Princeton graduate, he worked primarily in hydraulics and food processing. “He helped perfect the Frito and made the machine that packaged them,” notes Bocell. “He made the machine that canned Vienna sausages, which are canned under pressure.”
Long got involved in the construction industry when he collaborated in the 1950s with Philip N. Youtz and Thomas B. Slick on their development of the lift-slab construction technique, in which concrete floors are poured at ground level and raised with hydraulic jacks. Long went on to become president of International Lift Slab Corp., and would later serve on the American Society of Civil Engineers’ task committee investigating the 1987 fatal collapse of the L’Ambiance Plaza, which had used the lift-slab technique.
Long first met Gosselin on a vacation in Europe and was retired when Gosselin came to the United States almost a decade ago to market his quick-setting resin. “It started in his garage in Florida,” remembers Bocell. “My grandfather would build something, and Claude would say, ‘This could work.’ Doing this, he came up with the actuator so the gun would lock in the drilled hole.”
The result of Long’s garage tinkering was the patented injection pistol, a version of which is used by CGI Texas today. “Before, we were using two thin pipes and a rubber sleeve—drill two holes and hold it all in place with vice grips. What my grandfather did was automate that process.”
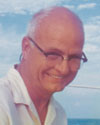
LONG
Using the device is simple. The pistol’s nozzle is inserted into a pre-drilled 1-in. hole. The knob then is pushed forward to engage the actuator, which expands to form a watertight seal around the opening. This allows for injections at up to 2,500 psi and also permits overhead and underwater work. The nozzle of the pistol can draw simultaneously from two attached tubes, allowing for two-component materials such as the CGI resin. It is driven by an air compressor and can be cleaned with water. The pistol also can be used for injecting epoxy, rust inhibitors, sealants or slurry into concrete. The pistol’s body is made entirely of stainless steel.
CGI Texas currently is selling the IP100 Injection Pistol as a stand-alone product through their website, although there are no plans to mass-produce them at this time.
The pistol’s powerful actuator allows for use in active leaks. “We called them in to seal some tanks, these 25,000-gallon tanks, some of which we weren’t able to drain beforehand,” says Josh Rowe, a manager at Water District Management, Houston. “They had to work with the water coming out, but once they got the resin in there it hardened and stopped. It’s pretty interesting stuff.”
Marshall Long passed away in 2005 at the age of 89. “He was always very proud of the fact he had met Einstein,” Bocell remembers. “When he was an undergrad at Princeton, his car had stalled and a professor walking on the sidewalk stopped to help him. He didn’t even realize who it was at first.”
Post a comment to this article
Report Abusive Comment