Warm-mix asphalt is hot. Asphalt industry officials believe warm mix, porous asphalt pavement and reclaimed asphalt pavement (RAP) will come to dominate paving in the next few years because the products offer lower costs and higher environmental benefits than traditional hot mixes.

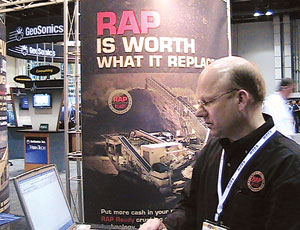
“The warm-mix revolution is starting to spread,” said Matthew Corrigan, asphalt pavement engineer with the Federal Highway Administration, addressing attendees of the Asphalt Pavement Conference on March 9 in Orlando. He noted that the number of states conducting WMA trials has increased from about a dozen in 2007 to all but a dozen now. “WMA is taking off—it’s just exploded,” he said. “Now the focus is on its evolution: the correct implementation on big projects and in high traffic.”
While year-old trials on Interstate 70 in Dillon, Colo., and in Yellowstone National Park have gone well, WMA is not a “magic solution,” he warned. Pavers must consider moisture, dwell time, types of additives, long-term performance and other issues. Several research projects are focusing on these issues.
WMA, already used in Europe, recently gained notice in the U.S. The first WMA conference was held in 2008, shocking National Asphalt Pavement Association officials when almost triple the expected 300 attendees showed up.
WMA is created from one of two techniques: one adds water to create a foaming bitumen, and the other uses a chemical additive. According to NAPA, WMA may also aid in compaction of highly modified binders and can allow for more cold-weather paving due to lower viscosity. It can be applied at as much as 100° lower than hot mix and allows for higher percentages of RAP.
Typically, RAP accounts for up to 15% of most asphalt mixes. According to NAPA, increasing RAP percentage to 20% to 45% in WMA mixes could mean a net savings of $4.55 per ton. “RAP is a process that makes good economic sense, and it’s green,” says Tim Harms, sales engineer with Kolberg-Pioneer, Yankton, S.D., which manufactures aggregate conveyors, rock crushers and other equipment. The firm was one of hundreds of exhibitors at the March 10-12 World of Asphalt/World of Aggregates show, which drew 5,700 attendees, up from 3,650 in 2007. Harms displayed a Website, www.berapready.com, that allows contractors to calculate cost savings using RAP in place of virgin aggregate.
Many other exhibitors also showcased products that reflected the WMA/RAP theme. Bagela USA LLC, Shelton, Conn., a subsidiary of the German manufacturer, exhibited its asphalt recycling unit. “Between going green, the cost of asphalt and continuing unknowns, there is a key interest in RAP,” says Greg Harla, sales director for Bagela. “We are still evangelizing the product. There were people here who didn’t even know it exists.”
Another firm, Ocean City, Md.-based NuStar, plans this construction season to offer contractors the ability to inject a chemical agent for WMA directly from its terminals into their asphalt trucks. “There’s no investment in equipment, no calibration,” says Ron Corun, asphalt technical support manager for NuStar. “They just send the truck in.”
Porous Pavement
Asphalt advocates are trying to spread the message that the material is environmentally friendly thanks to WMA, RAP and porous pavements. At the conference, Jim Huddleston, executive director of the Asphalt Pavement Association of Oregon, told attendees, “There’s no doubt in my mind that an open-grade porous pavement can handle heavy loads,” he said. “You just need to optimize the design.”
Although porous asphalt has been used in parking lots, its use in roads is still rare (ENR 2/12/07 p. 32). He cited a full-depth porous stretch on Arizona’s State Route 87 that carried 30,000 daily vehicles and performed for over 20 years. More recently, a 32-acre private development in Salem, Ore., used porous asphalt for its streets. An 8-in. layer of stone sub-base was topped by a 10-in. layer of porous rock that can hold up to 4 in. of rainwater. That was topped by 3 in. of asphalt-treated permeable base.
Post a comment to this article
Report Abusive Comment