...subcontract rod installation most likely this year. Rods will be drilled from chambers around each corner of the foundation block. To improve rod-placing control, intermediate smaller chambers will be drilled at three sides. A loggia on the east side precludes an intermediate chamber there.
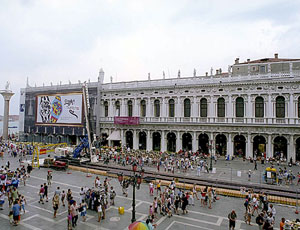
SACAIM hired Trevi to treat the chambers’ surrounding soil. Corner chambers will each have 10- to 15-sq-m plan areas of different shapes because of surface features.
Two or three rows of 40-cm-dia soil piles, cutting into each other, will form the 1-m-thick consolidated material of about 50 Newtons per sq centimeter strength, says Vanni. Columns, reaching 8 to 9 m into the ground, will form watertight chamber walls. Shorter columns will seal chamber bottoms.
In these conditions, high-pressure jet-grouting consolidation would have been more effective than mechanical deep mixing, says Vanni, but the designers “prefer not to use high pressure.” The Milan-based firms Studio Tecnico Macchi and Studio Geotecnico Italiano are handling design. The alternative consolidation method is “to mix with deep-mixing technology using injection grout at low pressure,” he says.
Months of discussions with civil servants went into selecting a drill rig that would cause the least damage to the square. Officials initially wanted a 10-tonne machine to be used but compromised on one just over 20 tonne, says Vanni. A rig of up to 100 tonnes normally would be used for deep mixing, he adds.
The chosen Soilmec SM 21 rig made its dramatic entrance last summer, crawling 160 m across the square on a protective runway of sand, neoprene and timber. After site trials, the rig began drilling at the north-east chamber a few weeks ago.
Columns are first drilled to full depth using minimum amounts of water—but no cement—to establish the extent of obstacles. “There are many obstacles,” says Vanni, citing buried construction materials from the tower’s long history. With obstacles eliminated, the column is drilled again, this time using cement and water.
The final operation involves rapidly moving the drill up and down to mix the column soil, because the bottom half of the columns are in fine sand and the top in cohesive, soft, organic material. “We need homogeneous columns,” says Vanni. Chamber bottoms are formed in the same way, but without grout being injected above the floor level.
Each wall column will be reinforced with a 9-cm-dia steel tube drilled through the column’s axis. Special sealing injections are planned to bond the consolidated soil with the tower’s structure, says Vanni. The four corner chambers will be lined with reinforced concrete and covered for long-term access.
Underground obstacles likely will impede Trevi’s progress, and the contractor also expects to lose time through periodic flooding. With St Mark’s Square’s paving set at around 0.9 m above mean sea level, Trevi will halt work whenever tides rise to 1 m elevation, says Vanni.
Venice Water Authority already has had the adjacent canal quay elevation raised to 1.1 m, but it has yet to obtain funding to waterproof the square itself, says a spokeswoman for CVN. The plan is to install drains and an impermeable membrane under vulnerable sections of the roughly 10,000 sq m of marble and trachyte flagstones.
But all this work is dwarfed by the vast project across the lagoon to install its three inlets and flood barriers. Funding snags have delayed the planned completion by two years to 2014. But CVN contractors are now casting caissons to house the gates. Adds the spokeswoman, they have recently completed assembly trials of the vast hinges of the 78 steel-box gates ahead of their mass production, the spokeswoman adds.
Post a comment to this article
Report Abusive Comment